Supply chain management
It is absolutely essential for the smooth operation of our business to be supplied with excellent technologies and services from our business partners. We are committed to ensuring fair transactions and appropriate procurement, and to working together to resolve various social issues
Procurement Policy(PDF:421.1KB)
CSR Procurement Guidelines(PDF:241.5KB)
Initiatives related to supply chain management
Responsible Raw Materials Sourcing
We have established the "Guidelines for Responsible Minerals Procurement" in recognition of the risks listed in Annex II of the due diligence guidance of the Organization for Economic Cooperation and Development (OECD) (conflict minerals in countries surrounding the Congo, cobalt-related child labor concerns, human rights abuses and labor issues in conflict zones and high-risk areas (CAHRAs), etc.) as a serious social issue in our supply chain. We respond to customers' requests for surveys by conducting risk analysis and assessment in cooperation with our suppliers.
*We use the Conflict Mineral Reporting Template (CMRT) and the Cobalt Reporting Template (CRT), Mica Reporting Template (MRT), Extended Minerals Reporting Template (EMRT)issued by the Responsible Minerals Initiative (RMI) as research tools.
Actual number of responses to request for surveys from customers through the TECHNO ASSOCIE Group in fiscal 2023;
total 295 requests (146 for CMRT, 16 for CRT, 15 for MRT and 118 for EMRT)
Communication with Business Partners
In line with the TECHNO ASSOCIE Group CSR Procurement Guidelines, we conduct awareness-raising activities that take into consideration the actual conditions of each supplier, and for those suppliers that we have identified as requiring support for improvement based on the results of the CSR Procurement Survey, we communicate with them and make proposals for improvement. Also in fiscal 2023, we held CSR procurement briefing sessions for main suppliers to inform them of the importance of working together throughout the supply chain to promote responsible procurement activities, including human rights due diligence measures.
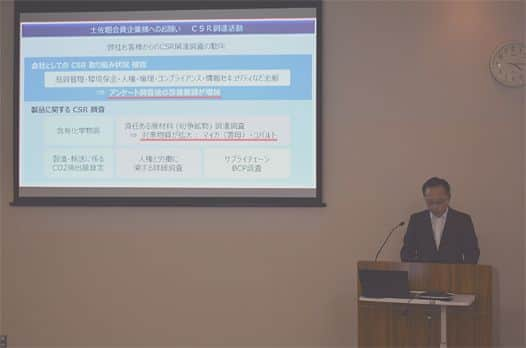
Diversity and Inclusion
TECHNO ASSOCIE considers human resources to be its most important assets and aims to be a company where everyone working for it can feel proud and rewarded. We help each employee improve and apply their knowledge and capabilities to achieve their own growth, as well as growth of the company, and ultimately contribute to society.
Examples of initiatives related to diversity and inclusion
Introducing a system to address diverse work styles and work-life balance
In order to accept the diversity of work styles and address the work-life balance, we are flexibly and swiftly examining and introducing systems, by considering the family circumstances and life stability of our employees, corresponding to the changes in society. In July 2023, we officially introduced the telecommuting systems that began as measures against the spread of COVID-19, allowing us to support flexible work styles while improving productivity. Furthermore, in April 2024, we introduced the Leave of Absence System for Spouses Working Overseas and Other Situations, allowing continued employment even when a spouse is relocated overseas. As part of our consideration for the stability of our employees’ lifestyles and family circumstances, we will continue to review and evaluate our systems flexibly and promptly in accordance with the changing times and in response to emergency situations when necessary.
Examples of system introduction
Examples of system introduction | Introduction of Regional limited course, job return system |
---|---|
Systems to Promote a Work-Life Balance | Telecommuting system, Staggered working hours system, short-time working system, System for leave during spouse’s overseas assignment. |
System to encourage leave-taking | Personally planned annual leave, Accumulated leave, Hourly paid leave system, Volunteer leave |
Addressing societal demands | Promotion of employment of people with disabilities, extension of the retirement age |
Certification as a Leading Company for Promotion of Women’s Participation and Advancement in the Workplace
In fiscal 2017, we were certified as a Leading Company for Women in Osaka City and Aichi Women's Brilliance Company. Under the "General Employer Action Plan" established under the Act on Promotion of Women's Participation and Advancement in the Workplace, TECHNO ASSOCIE has positioned promoting diversity as one of our key management strategies to maximize abilities of our diverse employees, and is working to promote female employee's active participation and advancement in the workplace.
Initiatives for Promoting Women’s Advancement and Participation(PDF:197.9KB)
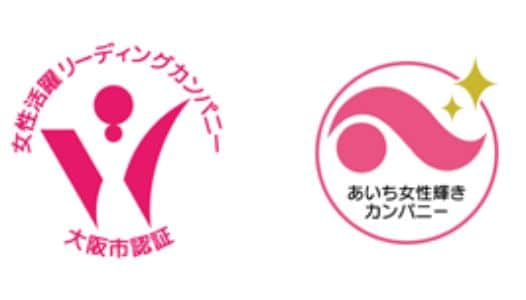
Commitment to Human Resource Development
We provide hierarchical training, which must be received on a position basis by all employees from executives to new employees, as well as thematic training, which aims to have trainees obtain specific knowledge and skills required in each section, and global human resource development training.
In addition, we position Corporate Principles and Business Policy, management policies and business conditions, safety patrols, compliance, human rights and harassment (including CSR) as priority training subjects and incorporate them into the curriculum of the training programs.
Communication with Employees
In the Group, we respect the freedom of association and the right to collective bargaining based on the laws and regulations of each country, and labor-management consultations about working conditions, welfare benefits, etc. are held on an equal footing. In recent years, we have placed a great emphasis on listening to candid opinions at our domestic sites through roundtable discussions and by holding individual interviews with young employees. The general manager of our Human Resources & General Affairs Department then confirms all the content of the hearings, and if necessary, we take measures to resolve issues that arose in order to promote the revitalization of workplaces.
Respect for Human Rights
TECHNO ASSOCIE Group Human Rights Policy
TECHNO ASSOCIE’s universal basic policy is to conduct fair business activities under high corporate ethics based on our basic spirit of Business Policy, Corporate Principles, and Charter of Corporate Behavior. We recognize that all of our business activities must be conducted based on the premise of respect for human rights as we continue to develop together with the global society, and we will continue to promote initiatives to respect human rights throughout the Group to fulfill our responsibilities.
TECHNO ASSOCIE Group Human Rights Policy(PDF:290.2KB)
Examples of human rights initiatives
Human Rights Due Diligence
Based on the “TECHNO ASSOCIE Group Human Rights Policy”, we conduct human rights due diligence throughout the TECHNO ASSOCIE Group and are carrying out further efforts to promote respect for human rights within the Group. After fiscal 2022, we put the focus on child labor, forced labor, and migrant labor with our affiliated companies and principal suppliers. Upon conducting an investigation, we addressed and corrected management practices in accordance with international human rights standards wherever risks were identified. We will continue to implement measures to improve human rights and work closely with our suppliers to ensure ongoing progress.
Human Rights Education and Training,Preventing Harassment
TECHNO ASSOCIE carries out human rights education with the goal of creating a corporate culture in which diversity is valued and employees have respect for each other’s human rights.
As part of the effort, we engage in continuous education and awareness-raising on the relationship between corporate activities and human rights through various in-house training programs (including e-learning).
Issues such as race, gender (including sexual minorities such as LGBT), religion, nationality, sexual harassment and abuse of authority are dealt with in the programs to strengthen the literacy of employees and teach how to respond when harassment actually occurs or is reported.
Implementation of Fair Recruitment
Techno Associe hires people in a fair and equitable manner to offer a variety of career opportunities, regardless of race, ethnicity, nationality, religion, age, gender, gender identity, sexual orientation, disability, etc. Recruiters participate in new appointment and basic training for staff in charge of promoting fair screening for recruitment and human rights enlightenment sponsored by Osaka Prefecture and incorporate what they have learned in their recruitment activities.
Basically, we are working on the premise that (1) we give opportunities to applicants widely and (2) we do not recruit employees based on anything other than the abilities and suitability of the applicants.
Human Support Contact
TECHNO ASSOCIE has established the “Human Support Contact” from the perspective of protecting human rights of employees, and worked to make it known to employees as well as appropriately solve issues. We have set up human support counselors at all of our domestic sites and hold training sessions every year at the area and organizational level to raise skills of employees in charge of the contacts and to enhance cooperation with the HR & Administration Department, an administrative office, in order to develop a system to allow employees to easily seek advice. Harassment Counselors Training was conducted where counselors learned how to prevent harassment from occurring by appropriately engaging with others, the importance of communication based on mutual understanding, and appropriate responses when receiving harassment consultation through role-playing as counselors. This training enables them to utilize what they have learned when they actually respond to consultations.
Occupational Safety and Health
Basic Philosophy on Safety
Safety is one of the core issues of operations at TECHNO ASSOCIE, together with compliance.
All those in a management position in the company follow the creed of ‘safety above all else.’ They strive to implement occupational safety and health activities with the understanding that safety is critical to all work processes, upholding slogans and adhering to the Occupational Safety and Health Policy and Occupational Safety and Health Regulations.
Occupational Safety and Health Policy
Employees' occupational safety and health constitutes the basis for a company's existence and a company has a social obligation to guarantee such safety and health. At Techno Associe and its partner companies, we respect each individual employee and put their safety and health at the core of our occupational safety and health philosophy. To put this philosophy into action, we implement the following policies.
-
1.Continuously improve occupational safety and health in company work processes and in the workplace environment, and build a healthy, productive workplace free of work-related accidents.
-
2.Comply with legal stipulations of laws related to environmental safety and health, as well as with in-house regulations, standards, and rules.
-
3.Provide education and drills to all employees (including those of partner companies) in order to boost their sensitivity to and knowledge of occupational safety and health.
This occupational safety and health policy will be periodically revised to ensure its effectiveness and its compliance with laws.
Occupational Safety and Health Slogan
Boost workplace occupational safety and health through resolve and action
Examples of Activities to Raise Awareness of Occupational Safety and Health
Safety patrols by top management
Every year during the National Safety Week in July, the company director in charge of safety and health gives a talk on safety in order to raise employees’ safety awareness. Directors also conduct annual work site inspections, with improvements made on items pointed out during the inspections in an effort to prevent accidents and create a more comfortable work environment.
Enhancing education
All new employees and mid-career employees receive safety and health training at the time of joining the company to enhance their awareness of safety. While a common type of accidents in our company was those involving property damage during work (company cars and forklifts), with regard to company cars, the number of such accidents has substantially declined recently as a result of providing annual e-learning training on safe driving to all drivers among our employees and organizing safe driving practical training at driving schools for young employees who are inexperienced drivers to help them improve their driving skills.
We have also taken continuous initiatives related to forklifts, such as regular lectures given by instructors from forklift manufacturers and improvement activities in warehouses, and the number of relevant accidents has significantly decreased as well.
All of our bases and affiliates in Japan take health-related initiatives including the activities of the Safety and Health Committee and health education by industrial physicians in an effort to raise awareness of health across the Techno Associe Group.
Preventing accidents while walking
Even in offices and other workplaces where there is nothing in their surroundings that causes serious occupational accidents, trips and falls on steps or other objects may result in unexpected injuries and accidents. In light of that, since 2018 we have been running a walking accident prevention campaign in an endeavor to raise employee awareness by reminding them of dos and don’ts while walking—namely, do not put hands in pockets, do not use a mobile phone, hold handrails on stairs, do not jaywalk, and look both ways before crossing.
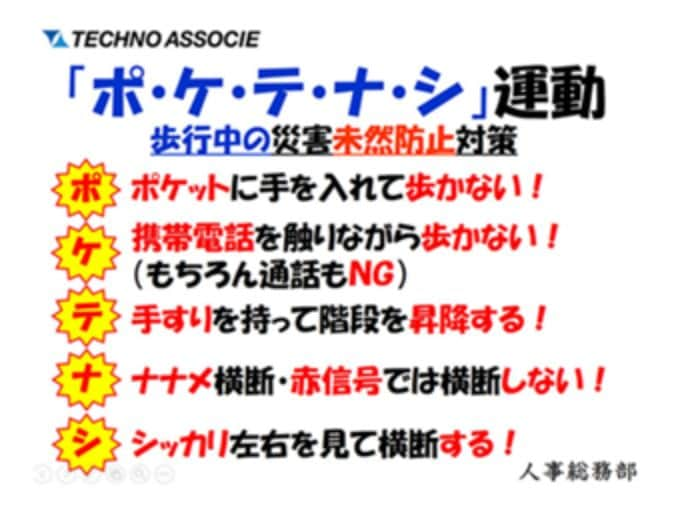
Safety and health initiatives at warehouses
Warehouses are workplaces that demand special attention to safety and health. To ensure the safety and health of employees working at warehouses and help create a better working environment, we have established Occupational Safety and Health Guidelines pursuant to our Occupational Safety and Health Regulations.
These guidelines primarily cover management structures, roles, education, guidance, and measures to be taken when injuries and other accidents occur, placing particular emphasis on the prevention of (i) heatstroke, (ii) backache, (iii) wounds from knives and other sharp objects, and (vi) trips and falls. Specific measures taken to prevent heatstroke include the installation of a clock with a wet bulb globe temperature (WBGT) monitor at each warehouse to alert workers of heat levels, taking breaks at appropriate intervals, replacing regular work clothes with those with excellent breathability and quick-drying properties, and providing neck cooling devices, air-conditioned clothing with fans, oral rehydration solutions, salt candy, etc. We are also working to prevent workers from suffering backache by supplying back belts, power-assisted suits and other tools. Thus, we are committed to reducing risks and preventing accidents.
For workers using machinery and other equipment, we have developed a safety management manual for each machinery and operation, which workers are required to comply with to work safely.
To familiarize workers with these initiatives, we continue endeavoring to raise safety awareness and improve working methods and environments by pursuing activities to enhance warehouse safety levels.
Health management initiatives
To enhance and support employee health, we undertake the initiatives outlined below.
- ①Regular checkups
- All employees must undergo regular health checkups in Japan. In particular, employees aged 40 or older are required to undergo comprehensive health checkups to examine more items in detail. Tumor marker tests, gynecological exams (cervical and breast cancer screening), etc. are also added to the test items to help detect lifestyle and other diseases at an early stage. If regular checkups detected potential problems in employees, we urge them to undergo a thorough checkup in collaboration with industrial physicians. In that way, we seek to make a regular checkup the opportunity for employees to look after their own physical health and start treatment early, rather than a once and done event. At our bases engaged in organic solvents and other operations that statutorily obligate the employer to conduct special checkups, we provide such checkups as required by the law.
- ②Health management education
- Educational sessions by industrial physicians are provided during monthly Health and Safety Committee meetings. In conjunction with this event, we are taking measures to maintain and promote the health of our employees by giving them opportunities to learn about health management, covering topics such as preventing heatstroke, influenza, and other infectious diseases, pollen allergies, and more.
Commitment to mental healthcare
Thinking that it is important for each one of our employees to recognize his or her stress levels (i.e., self-care) and for workplace supervisors to take appropriate action for mental health (i.e., line care), we are committed to the following:
- ①About self-care
- Mental health checks are conducted every year and all employees can use the services including those of domestic affiliates, and an “external counseling contact for mental health” that all employees and their families can use at any time has been established to promote self-care.
- ②About line care
- Emphasis is also placed on the line care of each workplace, and training is provided for supervisors. Workplaces with a comfortable and friendly atmosphere so that people do not get sick have been created and action is being taken in conjunction with personnel managers and industrial physicians.
FY2023 Occupational Accident Data (Non-consolidated)
Indicator | FY2022 | FY2023 |
---|---|---|
Frequency rate of work-related injuries*1 | 2.01 | 2.81 |
Severity rate of work-related injuries*2 | 0.00 | 0.05 |
*1 Frequency of work-related injuries and fatalities per 1 million total working hours
*2 The number of days lost due to work-related injuries per 1000 total working hours
Social contribution
TECHNO ASSOCIE Group Social Contribution Policy
The TECHNO ASSOCIE Group will not only contribute broadly to society by providing products, technologies, and services that are useful to society through its business activities but also actively engage in social contribution activities as a member of society for the realization of a better society in accordance with the “Corporate Principles,” “Business Policy,” and “Charter of Corporate Behavior.”
Community Service and Support in Fiscal 2023
As part of community service activities, we support various fields as shown in the following table through making donations to corresponding organizations.
Charity activity | Number of times | Amount |
---|---|---|
Support for Sports, Culture and the Arts | 4 | 925 thousand yen |
Support for Environmental Conservation | 2 | 1,016 thousand yen |
Support for Regional Activation | 23 | 20,405 thousand yen |
Support for Response to Humanitarian Crises | 14 | 4,393 thousand yen |
Support for Health/Social welfare | 2 | 130 thousand yen |
Others | 2 | 27 thousand yen |
Examples of initiatives related to social contribution
Donation Activities for Developing Countries
TECHNO ASSOCIE 's headquarters proudly supports the efforts of TABLE FOR TWO International, a specified non-profit organization that has been donating funds to cover the costs of providing school lunches in developing countries (Uganda, Rwanda, Ethiopia, Kenya, Tanzania, Philippines) since 2019. In this program, 20 yen (enough to pay for one school lunch) is donated for every healthy menu item sold in employee cafeterias. In fiscal 2023, donations from TECHNO ASSOCIE were enough to provide approximately 14,441 school lunches (more than 280,000 yen).
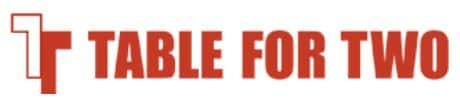
Support for Environment/Nature Protection Organization
We are making donations in support of the National Land Afforestation Promotion Organization's "Green Fund" and the World Heritage and National Treasure Kamomioya-jinja Shrine and the Tadasu no Mori (Tadasu Forest) National Historic Site environmental preservation and cultural asset conservation and repair project.
The Green Fund is working to create healthy forests that are connected to air and water, and to nurture the next generation through forests.
The Tadasu no Mori (Tadasu Forest), located in the Shimogamo Shrine in Sakyo Ward, Kyoto City, has the same vegetation as the original forest of the 3rd century B.C. The beautiful landscape that has been passed down for over 2300 years, and even buildings designated as national treasures and /or important cultural properties, which are in excellent traditional architectural styles from the Heian period, are in danger of being severely affected by rapid temperature changes and urbanization in recent years. We believe that the preservation of the natural environment is also important to protect the precious World Heritage sites for the next generation.
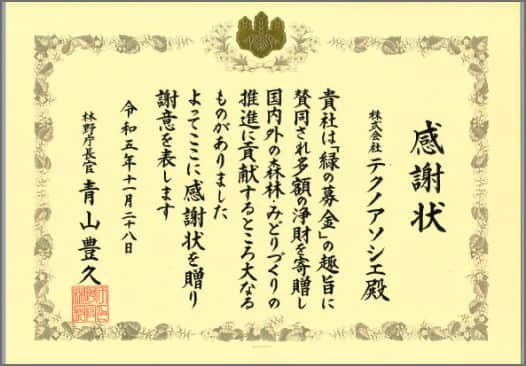
Green Fund Certificate of thanks
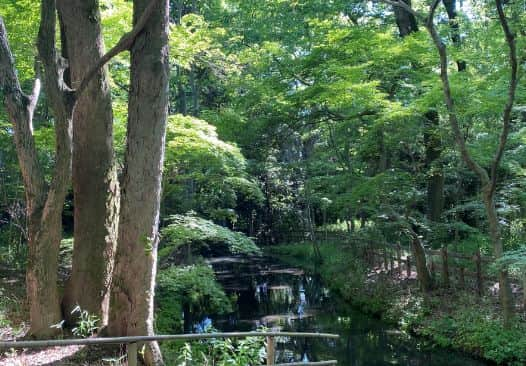
Tadasu no Mori